INDUSTRIAL IOT

OVERVIEW
Industrial IOT (IIOT) includes multiple areas – safety, security, productivity, wellness, environmental preservation, predictive and preventive maintenance, utilities cost reduction etc. IIOT is considered to be one of the most attractive IOT fields to practice since it actually provides HARD ROI to the industrial companies – a fact that isn’t obvious in other IOT verticals.
Following is an example of a simplified diagnostics system for predictive maintenance of manufacturing equipment. Predictive maintenance is the practice of determining equipment malfunctions before they occur and preventing unnecessary routine maintenance. Achievement of those two goals can save factories millions of dollars in expenses due to considerable reductions of machinery and equipment halts.
System methodology is based on the notion that a malfunction is a consequence of multiple and irregular factors that occur during equipment operation – i.e. a deterioration is gradual and hopefully measurable process. If the event that leads to a malfunction can be measured apriori – it can be avoided; and vise-versa – if such events are not detected, there is no point in performing a preventive maintenance.
Our simplified example is based on BIG DATA collection and analysis employing signal processing and machine learning technique. It includes the following modules and layers:
- Sensors layer : sensor infrastructure located on the equipment to measure parameters related to the specific machine – e.g. vibration (on motors), temperature, pressure, moisture. New machines may already contain those sensors; however, in many cases, sensor infrastructure needs to be added or augmented.
- Communication layers: data aggregated from the equipment needs to be collected and sent to the analytical platform which, in many cases, is cloud based. Even when the equipment contains local sensors – it doesn’t have the remote data transfer capability. Communication is divided into three sub-layers: sensors layer which uses wired communication to transfer data from sensors to a local sensors hub; endpoint layer which uses wireless local area network based on BLE 5.0 to transfer data between endpoints and nodes; node layer which uses wireless wide area network based on NBIoT / LoRaWan to transfer data from nodes to a cloud gateway. Note that communication system architecture may be different in other systems and use less layers.
- Processing layers: distributed computing techniques are used to process raw data coming from multiple sensors and machines in order to reduce the data rates between layers before final processing at the command & control level.
The final layer, which is cloud based, processes data coming from multiple sources, as-well-as historical data in order to visualize the operation of the equipment, provide statistics and business intelligence and predict hazardous events. Data from vibration sensors can, for example, pass through FFT filters and be analyzed in the frequency domain. A malfunction events may be triggered if the frequency differs from predefined thresholds
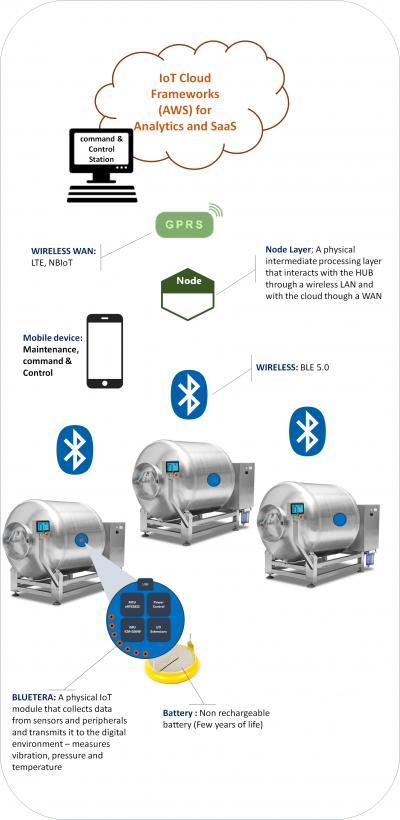